Actions to get your plant ahead of the curve
To get up to date, and ahead of the curve, when it comes to the latest food safety regulations, processors need to think beyond the current rules and consider what their customers demand. This requires more than simply following government guidelines; it requires an understanding of the marketplace and where the food and beverage processing industry is heading in the future.
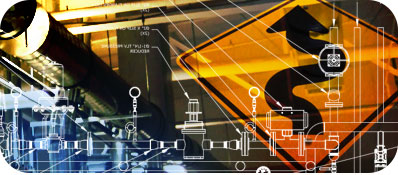
Wright Process Systems recommends that food and beverage processors of all sizes follow a basic safety upgrade plan to root out current liabilities and identify areas for proactive improvement:
Stage field audits to identify risk contributors. Discover what risks your current system has, and how they can be mitigated.
Implement equipment overhauls to meet current requirements. The requirements are constantly changing, but the current guidelines give a good roadmap what might occur in the future. Now is the time to update aging or non-compliant processing equipment before it’s mandated under strict government timelines.
Change process materials or components to higher-grade, sanitary versions. In many cases, existing systems can be upgraded with relatively simple—and cost-saving—material or component changes. Consult a process engineering expert to see if you can modernize your system without reworking it from top to bottom.
Rework piping systems to eliminate historically problematic practices. Process design-and-build companies like Wright Process Systems can help you reconfigure your sanitary process piping to both fix typical food safety problems and set you up for more efficient, more compliant processing in the future.
Upgrade automation and instrumentation for quality assurance tracking and self-checking. Today’s food and beverage processing moves fast. Can your system monitoring, maintenance, and recording pace? Automation and instrumentation upgrades not only improve your food safety monitoring procedures, they also help you save human resources with more efficient functioning that doesn’t require as much manual attention.
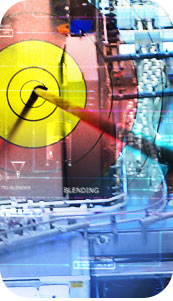
Improve managerial documentation for critical control points. With better automation and instrumentation comes the potential for better managerial documentation. If a problem does arise, or if a risk factor presents itself, better documentation helps your operational team identify the problem and address it at critical points in your process quicker and more effectively.
Retrain and coach operators for best practices. As your system advances, so should the knowledge base of your operators. Make sure your operators and facility managers are up to speed on the latest regulations, latest best practices, and latest equipment.
Wright Process Systems offers a unique combination of technical service expertise and onsite service proficiency to not only help you discover areas for improvement, but to also design and implement those improvements quickly, efficiently, and with minimal disruption to your operations. Contact us today to learn more.